Linyi DoMore Textile Technology Co., Ltd.
l DoMore low torque yarns are to create greater value-added space for the customers.
l 40% increase in production efficiency
l Saving of 335 KWH electricity in producing one-ton yarn
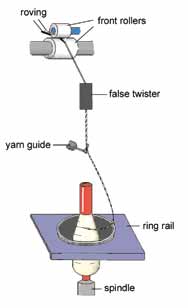
Nu TorqueTM Single Ring Yarn Technology (“Technology”) is an invention by Prof. Tao Xiaoming from the Institute of Textiles and Clothing of The Hong Kong Polytechnic University (“PolyU”) which is at present committed to the promotion of the technology to market. DoMore Textile Technology Co., Ltd. in Linyi High-tech Zone has seen achievements in the electronic numerical control technology and product development of low torque spinning technology through all-round cooperation with the University, achieving the transformation from technology to commodity. This kind of yarn presents such advantages as high efficiency, low cost, and added value for customers.
Technical innovations
A mechanical false twist device is installed in between front roller and guide wire of conventional ring frame to balance the fiber torque, the yarn produced from which enjoy higher tenacity of low twist, lower residual torque, as well as less hairiness and better evenness over the conventional one. Therefore, the yarn can be softer and smoother while maintaining high strength of textiles.
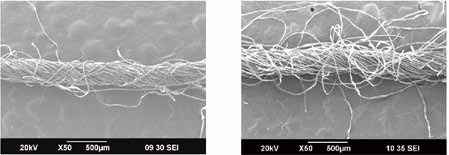
29tex (20 counts), 440 t/m 29tex (20 counts), 440 t/m Low Torque Single Ring Yarn Traditional Single Ring Yarn
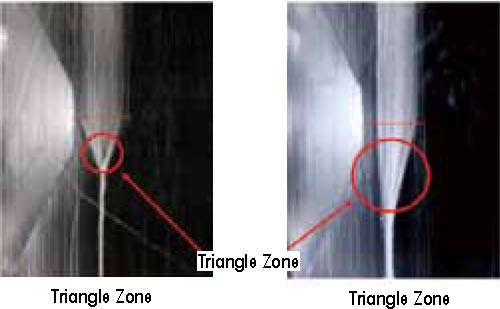
Triangle Zone
Performance advantages
In mass production of 7 – 100 Ne single yarn at a twist level that is 25% – 40% lower than the normal twist of ring spinning, its unique product features that such spinning techniques as ring spinning, compact spinning, solos-pun, and air jet vortex spinning are not equipped include:
l small torque of single yarn
l low twist and high tenacity of single yarn
l less spirality of cotton knitted sweaters
l unique cashmere-like feel
Range of application
The technology has been successfully applied to pure and blended spinning of various fibers including cotton, wool, cashmere, silk, modal, Tencel, viscose and kapok. It can be used to produce low torque ring-spun single yarn, slub yarn, elastic core-spun yarn, high-count hollow yarn, cotton vests, T-shirts, denim and towels. The knit fabrics from this yarn only contort a little after repeated washing, besides, they feel soft and have excellent anti-pilling and breathability; however, the woven fabrics, with flat and smooth surfaces, enjoy better tear strength, breaking strength and abrasion resistance.
Potential benefits
The Technology brings improvement to the overall throughput of a spinning factory by improving bottleneck operation in spinning process. It is estimated that the overall productivity of a spinning operation will be enhanced by 20% - 40%. The Technology enables the users to compete on the value and savings that are brought by the Technology, instead of price (Table 2).
Table 1 Performance Advantages of Low Torque Yarn
Performance Advantages |
Downstream Industrial Advantages |
Significant decrease of hairiness |
Production costs in waxing, singeing and sizing will be reduced accordingly. |
Improvement in evenness / thick and thin places |
The possibility of defects will decrease in downstream production processes, and the fabric surface defects are reduced, lowering the costs.
|
High tenacity |
The breakage rate will be reduced in the follow-up high-speed weaving and knitting process, significantly improving production efficiency.
|
Low torque and low twist |
Subsequent dyeing process sees improvement in efficiency, and the products are easy to color and dry.
|
The clothes feel soft and comfortable, with such characteristics as strong breathable and sweat-absorption effect as well as rapid drying after washing. For high-end consumers, the natural fabric can be used to achieve the sensory effects of chemical fibers, such as Modal, Tencel, and bamboo fiber. |
Table 2 Potential Benefits of the Technology
Yarn production cost |
• 24% - 40% increase in productivity
• 10% saving as no doubling and twisting |
Finishing |
15% - 20% finishing processes less than those in traditional cotton-woven fabrics |
Knitting |
10% saving in knitting cost due to lower spirality and clear surface with symmetrical loops |
Energy saving |
Saving of 335 KWH electricity in producing one-ton yarn |
Environmental protection |
No chemicals, no water and steam required for production |