Homemade knitting equipment: A win for excellence and precision
--- Interview with Lin Guangxing, Vice President of China Knitting Industry Association
Original by Liang Ruili, Translated by Xu Yuanyuan
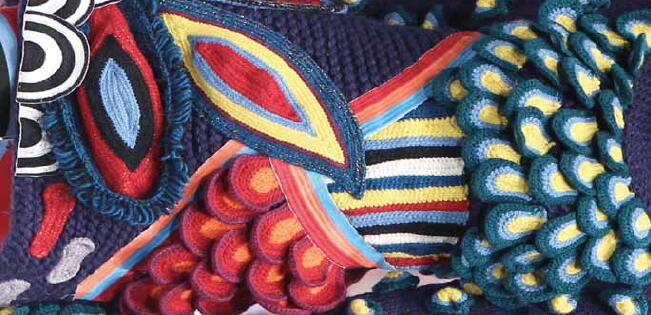
The manufacturing level of the knitting machinery improves, with respect to the circular weft knitting machine, flat knitting machine, warp knitting machine that all achieve the international advanced level in the scale of production, and especially possess the advantage of cost performance.
In the field of warp knitting machine, only by accelerating the optimal design can the warp knitting machine achieve efficient development. For example, in the process of loop formation, it is necessary to reduce the stroke of needle movement and swing of the guide bar. The machinery design must take into considerations the working stroke and specification parameters of the guide bars as well as structural optimization according to the requirement for production and the stability of operation. At the same time, the further consideration is also necessary for energy consumption and noise control when the machine operates.
In terms of the extension of warping function, traverse movement of the multiple-bar jacquard and electronic jacquarding can be realized by electronic control. Positioning jacquard is also made available to promote the function of jacquard, making the jacquard scale in rich patterns suitable for the requirement of clothing market. A variety of jacquard combinations change infinitely with the quality of many levels and the decorative patterns in full and realistic designs more delicate and perfect, making products rich and colorful after printing and finishing process to meet the requirements of high-end consumption.
The knitting equipment consists of circular knitting machine and flat knitting machine in the field of weft knitting machinery. Circular knitting machine is the main model of weft knitting production, which is suitable for processing natural fiber and chemical fiber into the fabric in large volume and variety. The application of domestic circular knitting machine improves steadily in the field of knitting industry, proudly with a batch of excellent and advanced domestic circular knitting equipments. The trend is that the proportion of equipment that has a 34- inch cylinder diameter has risen sharply. The manufacturing level of general model increased rapidly, and electronic jacquard, electronically controlled models have reached the advanced level in some area, meeting the user's requirements for high quality, style, personalized and high-end fabric.
The knit fabric is becoming light and thin, which is a direction of development, so the knitting machinery manufacturers launched circular knitting machine with high-gauge and fine needle pitch, for example, multi-runway circular knitting machines with type of No. E36 and above, going with the trend. In fine-gauge computer jacquard circular knitting machine for single jersey and double jerseys, the requirement is very strict for the precision of the machine manufacturing, computer control technology and mechatronics to meet the operation of electronic needle selection and speed response to the needle selector. The computer control technology includes electronic needle selection, electronic adjustment of yarn feeding etc. and they are still in the process of increasing application.
The improvement of the inlaid technique will provide richer intarsia patterns. By exchanging the back and forward position of the two yarn guiders to change the vertical angle of yarn lying, the yarn is plaited to reveal relationship between the yarn changes, resulting in different color-block effect. The knit-to-wear function of the computerized flat knitting machine allows for no further stitching process, and just for appropriate after-treatment. With this, it can become a finished product, which brings convenience to individual needs.
Besides optimizing the knitting equipments, there’s also need to improve the application of new materials. It’s essential to expand the application of high-tech materials and employ the materials helpful in increasing operation speed and stability, such as carbon fiber-reinforced materials, which are not sensitive to temperature for key components to reduce motion inertia effectively in the process of knitting.
Accelerating the integration of the industry and information technology is also a requirement of the device. By computer simulation design, it can optimize the motion curve of the loop-forming devices and the rationality of their interworking, reducing the gear acceleration of the partial machine, making the stitch-forming parts operate smoothly, therefore, suiting for high speed operation and improving operation reliability. By optimizing design for curve of disk chuck or cam in the traversing system, it is much assured that the traversing and loop-forming motion of the yarn-guide needles turns out to be more stable, satisfying the high-speed operation requirements. Electronic control technology is applied to lateral move (traversing), jacquard, warp, draw, take-up, weft insertion and auto-stop for broken yarn.
No matter what kind of the equipment, we need to ensure the quality of the product and increase operating efficiency and stability, in order to further implement the computer-based design, functional diversification, production with high speed, intellectualized control and simplified operations. In addition, how to achieve green and environmental protection, energy conservation and low-carbon as well as noise reduction is also a challenge that the enterprises should stand the test of.
With the increased demand for knitting machinery, it is all the more urgent to strengthen linkage between the machinery manufacturing and knitting production sectors. For that endeavor, “National Vocational Skill Contest for Weft- knitting, flat -knitting and Warp- knitting Operators” has been organized for many years since 2011. The national finals all adopt domestic circular knitting machine, computerized flat knitting machine, and warp knitting machine, it’s an effective way to achieve the combination between equipment manufacturing on supplier side and practical application on client side. Through the contest that examined the performance of domestic equipment, players put forward effective proposals for equipment improvement.