Reform and restructuring for a new CHTC
By Zhao Zihan
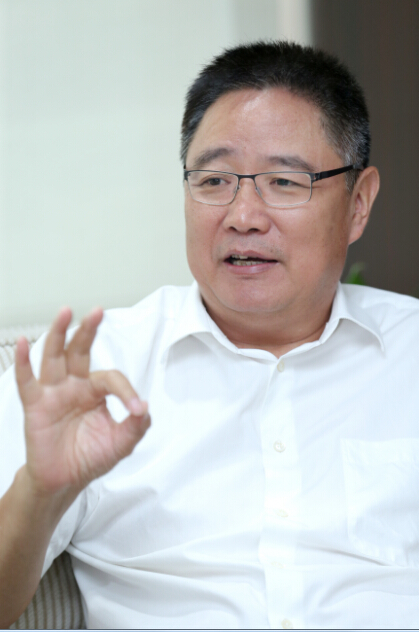
Zhang Jie, President of CHTC
“What has China Hi-Tech Group Corporation (CHTC) done in recent years?”
“CHTC has been engaged in one thing for these years, i.e. holding the ground of textile machinery as main business and building competitive advantages for the industry and the enterprises in the state of full market competition.”
As the “aircraft carrier” of domes-tic textile machinery industry in China, CHTC is a deservedly industry leader on the road of developing advanced equipment manufacturing industry and promoting the manufacturing industry from big to powerful. The group is equipped with world-class advanced technologies and industry-leading R&D direction in various fields of textile machinery manufacturing, winning an important position for China in the world textile machinery manufacturing industry.
During the 12th Five-Year Program period, CHTC enjoyed satisfactory achievements based on own adjustment and transformation. Moreover, CHTC has been adhering to the development strategy of “changing its single business mode of textile machinery for a related multiple-line operation”, witnessing various degrees of development in the fields of textile machinery, textile trade, new fiber materials, commercial vehicles and engineering machinery, financial investment, culture, real estate, and asset management.
At the upcoming 17th ITMA taking place from 12th to 19th November 2015 at Fiera Milano Rho in Milan, Italy, CHTC will organize its domestic and overseas textile machinery manufacturing enterprises to participate in the exhibition together with exhibits covering such fields as cotton, chemical fiber, dyeing and printing, weaving, and non-woven, fully displaying CHTC’s strength in the textile machinery field. In this respect, Zhang Jie, President of CHTC, received the interview from China Textile, making an analysis of CHTC’s performance in the 12th Five-Year Program period as well as the future development of China’s textile industry, and focusing on a detailed elaboration on the reform and restructuring of the Group.
CHTC has 22 secondary subsidiaries and 5 listed companies at home and abroad. During the 12th Five-Year Program period, CHTC’s textile machinery business was expanded from cotton spinning and chemical fibers to dyeing and printing through purchasing of Fong’s, and to the nonwoven business through acquisition of Autefa Solutions Germany GmbH. Thus, CHTC has been growing into an enterprise of the largest business size and the most complete varieties of textile machinery in the world.
As we all know, textile industry, as China’s important livelihood industry, matters a lot whether it is under a healthy and sustainable development. In this regard, Mr. Zhang said: “As a large-scale central enterprise, CHTC cannot just pursue a maximum of profit, but must undertake certain social responsibilities; otherwise the textile enterprises will have to bear the pressures. If only CHTC can keep a healthy development, well raising the banner for China’s textile industry.”
In recent years, CHTC has seen a lot improvement in manufacturing capacity and innovation ability of textile machinery, well supporting the progress of Chinese textile enterprises; however, it has not enjoyed optimistic profitability in its main textile machinery business. In this regard, Mr. Zhang believed that CHTC must insist on doing the right thing and the main textile machinery industry can be financed from other areas. At present, the most important thing is to carry out industrial layout and structural adjustment, which reflects not only the ability of a state-owned enterprise to resist risks, but also the responsibility of such a company to undertake.
Elaboration of reform
▪ For the needs of Group strategy
Mr. Zhang summed up the three-step development strategy of the Group: “go complete”, “go excellent”, and “go powerful”. The first step is to recreate a CHTC which will see a change in growth from quantity to quality as well as a transition to professional management. The key of the second step is to pay attention to the intrinsic quality, and to this end, the Group put forward a change from three major business sections with six business units to “One Body with Two Wings”. As for the third step, Mr. Zhang believes that “The Group will go powerful as long as the resources are well integrated and the internal businesses are straightened out.”
China Textile Machinery (Group) Co., Ltd. was established as a future operation management platform to include all of the textile machinery business in CHTC. According to Mr. Zhang, CHTC textile machinery business goal is to be the most powerful globally from the biggest in size in the world, and now the Group has basically reached this goal.
▪ For the changes in the development of the industry
“Please do remember the year of 2015. It is a year in which textile industry is going towards a higher degree of industrial concentration from the full competition in a traditional way.” Mr. Zhang continued emphasizing that “The transformation today is different from the past when the focus was on volume rising, aiming to a higher level and a larger scale. For example, in cotton spinning industry, so many enterprises are suffering no orders, however, the supply of orders to CHTC fall short of the demand. Why are so significant differences under the same competitive pattern? The large-scale enterprises would like to use the equipment of the best performance ratio based on the current pattern of changes, and the practice has proved that those who adopted CHTC set equipment and technologies will establish a better competitive advantage and enter a good momentum of healthy development. CHTC has achieved a complete flow scheme of the industry, greatly improving production efficiency and saving energy costs. CHTC has also seen changes in the mode of service, ranging from installation and after-sales service to the future maintenance service. In addition, there are also supporting financial and market services. In order to enhance the overall capacity of coordination in all aspects of the services, there is an urgent need to put all aspects together.”
▪ For the overall requirements of adapting to the following international development
CHTC is now equipped with “a strategy of one body with two wings, supported by a triunity management and control model”.
The so-called “triunity” consists of three parts: directors & supervisors, managers, and shareholders. Centering on such five core functions as human resources, strategic management, budget management, risk control, and information construction, and focusing on core business while developing the strategic businesses, CHTC has conducted allocation of resources to the strategic goals as well as the short-term, medium-term and long-term objectives in line with the Group’s long-term development. Subgroups are created from the individual business areas. The performance evaluation criteria are established from the four dimensions of EVA, business and market share, labor productivity, and technological innovation to help them fully participate in market competition, achieving profitability and asset value enhancement as well as brand and social value promotion. As for the business strategy between the Group and the sub-groups, the directors and supervisors of the sub-groups are appointed by the headquarters, while the professional managers are hired by the sub-groups themselves, realizing a parent-subsidiary company governance and control system.
“One Body with Two Wings” refers to the high-end manufacturing as the body and the financial and cultural industries as the two wings.
High-end manufacturing contains three main businesses: textile machinery, new energy vehicles, and new industrial materials, of which textile machinery is to became the most powerful in the world from the largest in size globally, which is also an unswerving goal of CHTC.
“3 dimensions” escort Chinese textile industry
As an industry leader, how does CHTC better enhance the international competitiveness of China’s textile industry while practicing its own development strategies? Mr. Zhang stated that it depends on the following three dimensions, the same as the challenges that this industry is facing.
“The first dimension, also the most important one, is technical support. It is a must for CHTC to attach great importance to technological innovation to improve industrial competitiveness for better and more powerful six business units.” Textile machinery manufacturing is the main industry of CHTC, directly affecting the overall competitiveness of China’s textile industry. In subsectors, CHTC is equipped with the manufacturing capacity in the sectors of cotton spinning, dyeing and printing, chemical fibers, and non-woven fabrics. Enhancing industrial competitiveness is required to start from the industrial demand. In the future, CHTC must focus on providing digital and intelligent equipment that can better satisfy the industrial development.
The second dimension is to undertake industry responsibility to accelerate development of new materials. CHTC owns the best chemical fiber equipment manufacturer, and has more practical experiences in the production of new materials. Currently, CHTC is actively increasing new materials development, focusing on the development of the three products of Lyocell fiber, lignin fiber, and polylactic acid fiber.
At present, Lyocell fiber costs lower than the conventional viscose fiber by 20% to 30%, and most importantly, the former is free of chemical reaction and pollution, enjoying broad industry prospects.
Polylactic acid fiber can be suitable for various fields for its functions of natural degradation, inflaming retarding, acid and alkali resisting, good warmth and moisture absorption.
Lignin fiber has brought a new approach to the development of low-cost raw materials. Mr. Zhang made a calculation that: “In China, corn cobs only are able to be converted into almost 8 million tons of fiber, which doubles the yield of cotton. Moreover, the maize straws are three times of the corn cobs, and if the inside lignin fiber can be used for carbon fibers or other fibers, thirty million tons of fiber will be made only from the maize straw. How large the figure is! China is a large agricultural country, and textile industry is big with wide range of materials, if the grass and branches can be recycled for further development, China’s textile industry will suffer nothing in raw materials.”
For the development of new materials, CHTC has already invested several hundred million yuan, and facing various queries, Mr. Zhang fervently believes that the path is correct. “In fiber field, the enterprise strength is not strong enough at present. But what CHTC is focusing on relies on technological innovation capability, aiming to provide greater potential for the development of enterprises.”
The third dimension is brand innovation capability. Currently, CHTC has founded a national fashion creative center in Songzhuang, with a purpose of not only serving the brand, design and marketing of textile industry but also going to deliver the profound meaning of Chinese culture and the concept of CHTC. “China needs such a platform and carrier like fashion creative center to gather people engaged in cultural creative in the world, for the integration of the industrial chain and innovation of the industry brands.”

Palletizing Robot System
Automation solutions
With the sustained and rapid development of textile industry, modern textile technology will be electronic information technology and intelligent production as the main feature. Therefore, our company developed automated logistics technology to improve cotton automation. The main product includes automatic guided vehicle, palletizing robots and automatic packer.
Palletizing robot is new generation intelligent automatic palletizing equipment. The robot inherited original technology and intellectual property, considering the needs of users, introducing international latest relevant technology. The robot is Cartesian robot with the features of high positioning accuracy, space trajectory easier to solve, and simple control. By laying rails on the ground, the robot can move between multiple machines to complete the task of yarn stacking. Robot also has automatic fault alarm functions to ensure safety during operation. In addition, the relevant components can be flexibly configured according to user needs, to meet the diversity of needs of users.
Technical Specifications
Technical Features
l The robot is Cartesian robot with the features of high positioning accuracy and simple control.
l By laying rails on the ground, the robot can move between multiple machines to complete the task of yarn stacking.
l Robot has automatic fault alarm functions to ensure safety during operation.
l Assemble flexibly and freely select the relevant parts according to the customer.
JFT1511 Soft and Smooth Ring Spinning Unit
The soft and smooth ring spinning (SSR spinning) is a unit that can be mounted onto all kinds of ring spinning frame. After drafting, it can soften the fiber at the spinning triangular space to lower the fiber modulus, change the fiber performance, reduce the hairiness and make it smoother.
Main structure
-
SSR spinning has two parts: soft and smooth parts, electric parts
-
The soft and smooth parts include: soft and smooth ceramic component, electric drainage controller, supporting seat, special seat for roller, etc.
-
Electric parts include: master power switch, socket compound, electric cable box, etc.
Applications
-
It is suitable for high-rigidity ramie fiber. For pure ramie yarn, the 3mm hairiness can be lowered by 60%.
-
It is suitable for many kinds of chemical short fibers. For viscose yarn, the 3 mm hairiness can be lowered by 65%.
-
It is more suitable for knitting yarn. For the pure cotton knitting yarn, the 3 mm hairiness
Jingwei E-system
Jingwei undertakes the National Science & Technology Pillar Program of the National Ministry of Science and Technology during the Eleventh Five-year Program Period. The “textile equipment network monitoring and management system” developed by the company realizes the digital management of the cotton spinning enterprises during cotton production process. The system not only integrates production process monitoring, energy management, environmental monitoring, personnel scheduling, quality control and other functions but also realizes the seamless integration with the ERP system. Up to now, the system has been applied to Wuxi Yimian, Luthai Textile Co., Ltd., Huafu Holding Pte., Ltd., Yunjin Textile Group, Jiangsu Yueda Group Co., Ltd., Shandong Ruyi Group and other leading domestic cotton spinning enterprises.
Advantages
As an equipment manufacturer with years of design experience of textile equipment, the company has a better understanding of textile equipment, and has many talents in mechanics, electrics, process, management and other aspects, which lays the foundation for emergence of e-system. In addition, years of experience in electronic control enables Jingwei to solve problems caused by high temperature, high moisture, high interference and other environmental factors. The system takes production as mainline, covering various parts such as workshop personnel, equipment, energy, quality, environment, order form, production scheduling and so on, bridges information islands in various links, achieves information sharing, and creates effective workshop production & management mode.
Benefits brought to enterprises
-
Exactly grasp status of production, improve accuracy of delivery, keep in-plant distribution logistics in order, and achieve cooperation in production, supply and marketing;
-
Accurately grasp amount of work in progress, trace rejects, and reduce production cost of work in progress;
-
Trace serial number of products by means of bar code, RFID and so on, collect complete data and process quality information, and improve level of after-sale service and degree of satisfaction of products;
-
Promptly reflect quality problems, trace history of quality, improve quality of products;
-
Reduce artificial statistics and manual report, and improve productive force of site administrator;
-
Fully grasp service condition of tools, equipment and so on, take advantage of manufacture resources effectively, etc. can be lowered by 60%.
JWF1418A Auto-Doffing Roving Frame
JWF1418A Auto-doffing Roving Frame adopts the DSP, servo and frequency control technologies to constitute a control system, realizing digital control. It employs a built-in automatic doffing system that realizes doffing, bobbin exchange, generate thrum and start-up in a full automatic way, enabling automatic spinning.
Uses the built-in automatic doffing system
JWF1418A uses the built-in automatic doffing system, invents a new doffing mode that can replace the full-yarn bobbins at both sides of the flyer with empty bobbins, realizing full-automatic spinning that includes doffing, bobbin replacement, Generate thrum and start-up.
Tail yarn clearing
The tail yarn clearing device is not connected to the roving transportation system, but directly mounted on the frame. For this reason, all empty-full bobbin replacement and bobbin cleanness can be conducted simultaneously in two parallel positions. The tail yarn clearing device cleans three roving bobbins at a time. Processed roving is inhaled into the storage box after full opening, and then the storage box is automatically emptied. In most cases, these opened roving will be used in production once again.
Empty-full bobbin exchange device
Tail yarn clearing and empty-full bobbin exchange device integrates tail yarn clearing, bobbin filtering and selection, as well as empty-full bobbin exchange. The “Empty-full bobbin exchange device” technology implements the replacement between full-yarn bobbins on the roving frame and empty bobbins on the transfer system; and realizes automatic transmission of bobbins by the Roving-Spinning Link transfer system.
JWF9562A Roving-Ring Link Conveying System
JWF9562A Roving-Ring Link Conveying System is the established between a rovings and spinning process can be realized online monitoring, information collection and analysis, automatic control and continuous delivery of three-dimensional space logistics lines, its basic function is to rovings three-dimensional space transmission lines, to send the full package rovings roving machine falling cheese to the full storage, to be issued a demand signal and then spinning the barrel full of rovings sent spinning, spinning run the empty pipe back to the empty tube storage, to be roving frame will then issue a demand signal to the empty tube control roving frame, to achieve Roving-Ring Link Conveying System Union.
Guide: By a high-strength aluminum alloy made, a closed section of the track, to prevent the accumulation of pollutants.
Conveying chain: The aluminum alloy bar chain, high-strength plastic hinges and integrated trolley carriage composed of freely rotatable in both horizontal and vertical directions, run sliders, no vibration and noise.
Shifting fork mechanism: For transporting commutation shift fork mechanism, there are two forms of manual and automatic. Automatic shift fork by cylinder control, positioning and reliable to ensure accurate transmission lines.
Control: High quality detection switches, intelligent and accurate delivery of each root yarn feeding rails.
SMARO-I Auto-winder Linked with Spinning Frame
SMARO-I automatic winder linked with spinning frame, is a new generation automatic winder developed by Qingdao Hongda Textile Machinery Co., Ltd. The winding speed can reach up to 2,200 m/ min. Adopting advanced control technology, the winding techniques and yarn track are designed in a brand-new way, thus its mechanical structure is simplified, air loop is better controlled and the electric intelligence is improved. The machine adopts global monitoring to obtain yarn with higher quality and more profit to improve the productivity largely.
High quality
Automatic bobbin feeding from spinning frame to auto-winder improves yarn cleanness and avoids yarn contact damage.
High efficiency
To solve the friction between package of spinning frame and speed so as to enhance the spindle speed of spinning frame and increase productivity.
Enhancing automatic level, saving manpower
To transport yarn package and feed bobbin automatically so as to save labor and connect the two labor-intensive procedures directly not only to realize automation and continuous production but also to improve quality and enhance productivity.
Completely Automatic yarn supply
-
Bobbin supply from spinning frame to auto-winder is completely automatic, free of manual feed. Behind single spindle it is designed with spare bobbin convey channel;
-
Bobbin conveyor increase logic judgment to make following actions such as full bobbin, empty bobbin, piecing, re-piecing, waste yarn treatment, stop, pass in CBF not interfered with each other;
-
Bobbin change is automatically detected and feed;
-
Empty bobbin is automatically transported back to spinning frame by loop belt;
-
Bobbin is transported by support disc that eliminate bobbin yarn surface damage and reduce pilling increment.
XORELLA XO TREND
Established in Switzerland in 1967 XORELLA has stood at the forefront in yarn conditioning and heat-setting ever since. Superior technology, reliability and precision were the foundation for the success throughout almost 5 decades. About 1,500 machines were sold to customers all over the world up to now. Since 2002, XORELLA has been a member of the CHTC Fong’s Group. With the XO SMART and XO SELECT series launched at ITMA 2007 in Munich demands of our worldwide customers can be satisfied from small capacity and manual handling to fully automatic vessels integrated in transport automation and packing systems from various suppliers. All machines feature the energy saving XO-heating system and can optionally be equipped with the waterless vacuum system XO Ecopac for maximized savings of precious resources. At ITMA 2015 XORELLA launches XO TREND, a new machine series to complement XO SMART and XO SELECT. This new machine series for all low temperature applications incorporates all renowned features of XORELLA machines. New benefits include:
-
Rectangular shape offering app. 20% better usage of inside space
-
Pin trolleys and pallets up to 1800 mm height can be used
-
Reduced energy consumption compared to cylindrical vessel
-
Improved insulation and cladding
-
Smaller pit area compared to cylindrical vessel of similar capacity
-
Pit depth for the vessel reduced by 50%, same pit depth like automatic loading platform
-
Optimized construction of all components
THEN AIRFLOW® SYNERGY 8
Aerodynamic High Temperature Piece Dyeing Machine
The latest generation of the THEN AIRFLOW® SYNERGY 8 is the best example of how to make good things even better. It is well known that the liquor ratio achieved with the THEN AIRFLOW principle up to date has not been beaten. The same counts for the versatility of this superior machine. With the latest development the energy consumption is further re-During ITMA 2015 XORELLA’s staff will be available in 2 Stand F109 for further information on the product range. With the new XO TREND and the well-established XO SMART and XO SELECT XORELLA offers efficient and reliable solutions for any conditioning and heat-setting requirements.
duced. Every tube now has an individual frequency controlled blower with less installed power. All the other advantages of the THEN AIRFLOW SYNERGY series remain unchanged, which leads to shorter cycling times and substantial savings in water as well as high reproducibility and smooth fabric guiding. Breaking the barrier of loading capacity, the model extends up to 12 tubes with individual control, suitable for various kinds of fabrics with better flexibility, quality and ergonomics.
MONFORTS FONG’S MONTEX
Stenter Frame Range
With technology support by A. MONFORTS in Germany and high production capacity in China, there are more than 2,000 sets of MONFONGS stenter frame as well as other ranges in service for customers since its establishment in China in the Year 1999. From launching the cutting-edge stenter frame range MONTEX 6500 in 2010, this new model machine has attracted wide attention in the industry and is in service to main textile base worldwide, such as India, Bangladesh, Turkey, Central and South America and South-east Asia, which led to a substantial market share and first-class reputation for Monforts Fong’s expansion in the overseas market. Being an outcome of long-time empirical knowledge and research of A.MONFORTS, this advanced stenter frame comes with distinctive features.
-
The machine applies PLC control system with Qualitex 750 software which allows long-distance technical support;
-
Automatic production process control system -Monformatic Professional;
-
Ergonomic design for operating with safety and comfort;
-
TwinAir system and heat recovery system are equipped to further reduce energy consumption and to contribute to superior production efficiency.
-
Optional nozzle types give wide adaptability to textile technology, which conform to the environmental-protection concept of energy conservation and consumption reduction.
THEN SUPRATEC LTM
Long Tube Machine
Over the years many improvements were made to make the THEN-AIRFLOW® technology even more efficient. However, in times of shorter batches in fabric dyeing the main requirement is flexibility and the fabric weight range. FONG’S EUROPE GMBH is presenting at ITMA 2015 a dyeing machine that can accomplish to handle a whole range of fabrics; from sensitive products up to heavy weights. It’s called “THEN SUPRATEC LTM”. The combined knowledge and experience of FONG’S and THEN led to a series of new and groundbreaking ideas: The “THEN SUPRATEC LTM” is a hydraulic long tube dyeing machine with a variable liquor ratio from short in the semi dry mode up to long in the wet mode. Variable angle, defined plaiting without any winch and a liquor ratio which is setting new standards in long tube dyeing are just a few features. The machine is able to dye woven and knitted fabrics, made of natural, man-made fibres and blends. The weight range goes from 25 g/lm up to 380 g/lm. Its high flexibility in terms of liquor ratio and the variable angle of the kier results in considerable savings in additives, water and energy. The current speed range goes from 80 to 600 meters/min. -depending on the fabric type.
Some additional features are:
-
Liquor ratio 1 : 5.5 up to 1:15 depending on the variable angle of the kier.
-
Low power consumption due to variable kier angle.
-
Up to three jets per tube with up to 1,000 meters each.
-
Up to four tubes with coupling.
-
Variable nozzles.
FONG’S TEC SERIES
High Temperature Piece Dyeing Machine
New generation of TEC series High Temperature Dyeing Machine, the state-of-the-art design achieved “Low Cost, High Quality, and Environmental Protection”. It is suitable for different dyeing process with various types of natural, synthetic, blended fibers, aiming to provide complete solutions: “Efficiency, Energy Saving, and Environmental Friendly”.
Main Features
-
Efficiency (Versatile Application): TEC series is specially designed for fabric which is having tight and crease marks sensitive structure, such as 40S/2, 26S/1, 20S/1, tightly knitted fabric, and sensitive shade (E.g. Turquose)
-
Energy Saving: With various new functions, cotton reactive dyeing process takes about approximately 248 minutes for light color
-
Environmental Friendly: The water consumption for reactive dyeing cotton fabric is lowered to 27.5, 37.8 & 47.6 L/Kg for light, medium & dark shade respectively.
-
Capacity: The new TEC Series offers at loading capacity of 300kg, 250kg 200kg per tube. Customer can choose in range of 1-12 tube.
-
FC30 color multi-function controller: By the Fuzzy Logic temperature control function, the dye liquid temperature deviation can be minimized at + / -0.3 ° C.
-
Patented design - “Lint Collector”: Specially designed for loose structure type such as terry towel and fleece; the collector can accumulate lint at the bottom and discharge it during draining.
Technical Data
-
Design Temperature: 140 °C
-
Design Pressure: 3.0 bar
-
Heating gradient: 25 °C -100 °C approx. 5 °C/min 100 °C -130 °C approx. 2.5 °C/min (dry saturated steam pressure at 7bar)
-
Cooling gradient: 130 °C -100 °C approx. 3 °C/min 100 °C -80 °C approx. 2 °C/min (cooling water at 3bar, 25 °C)